Auditing is a crucial tool for ensuring that laboratories run successfully and efficiently. In a regulated context, this article will examine audit results pertaining to equipment/Instrument management systems. It will specifically look at the difficulties with these systems and how laboratories can enhance their equipment management systems to satisfy regulatory obligations.
- Failure to document and investigate discrepancies;
- Failure for adherence to change control system of instrument;
- Instruments which were installed were not sufficiently qualified (IQ, OQ, PQ);
- Organization does not have Computer System Validation Philosophy / Plan;
- In production department, cleaning failures observed, which were not fully investigated.
- In production department, Filters used to sterilize bulk drug solutions are not being subjected to a pre-filtration integrity test;
- The usage of obsolete SOP for maintenance and calibration of the concerned instrument by the appropriate person
- The absence of History records for the instruments to document when routine repairs and replacement of parts is performed;
- Absence of SOP or any written processes for calibration and preventive maintenance of laboratory equipments.
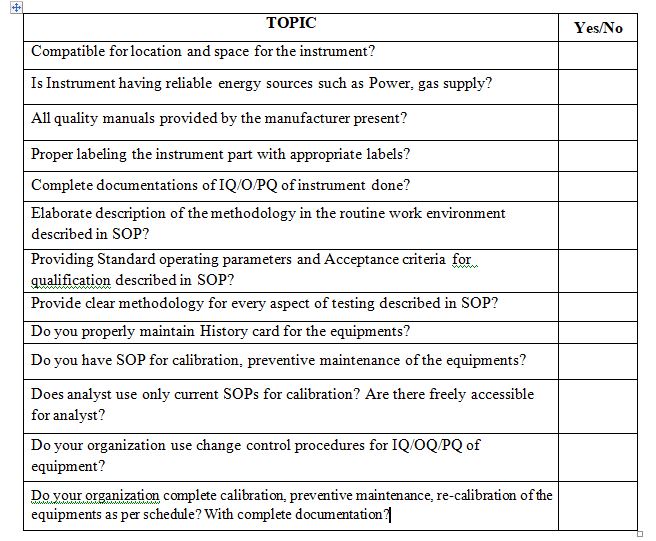
After reading this blog, we hope you can understand the importance of equipment maintenance and properly use the proposed checklist and improve on it further.
Now that you know this:-hopefully you are in position to answer the Assignment(s)
Please review the IQ/OQ/PQ of recently installed equipment in your laboratory?
In your lab, do IQ/OQ/PQ are properly archived? Further easily retrievable at the time of requirement?
In your lab, quality manuals submitted by Vendor is stored properly and accessible to analyst at the time of requirements?
Does SOP design based on IQ/OQ/PQ of the instrument?
Does SOP incorporate preventive maintenance and calibration as per IQ/OQ/PQ or vendor recommendations?
Is training of laboratory staff part of new IQ/OQ/PQ?