Installation Qualification (IQ) is a process that ensures the correct installation of systems, equipment, and software in a pharmaceutical production facility. It is a crucial step in the validation process and is used to confirm that all system components are set up and configured correctly in order to satisfy the needs of the intended use. This article provides a checklist to help ensure that your installation qualification activities are properly conducted.
For effective instrument qualification, the installation must meet a manufacturer necessity which includes:
- Compatibility of the location and space for the instrument.
- Instrument should have reliable energy sources such as Power, gas supply.
- Compatibility of Environmental and operating conditions for the instrument.
- Physical verification of newly to be installed instrument for any external damage
- Physical verification of contents of the instruments against the packaged list/pre-agreed list.
- Collection of all the quality manuals provided by the manufacturer.
- Collection and verification of primary and secondary calibration standards.
- Verification of software-installation along with original DVD/CD of application software.
- Proper installation of instruments accessories and its sub systems.
- Installations of all necessary connections and communication with accessories sub-units.
- Verification of software versions and firmware versions along with key numbers.
- Proper labeling the instrument part with appropriate labels.
- Complete documentations of dates used for installation qualification of instrument.
In summary, Installation Qualification checks the important elements installation.
US FDA Recommendations for Installation Qualification 21 CFR 820.70(g):
- Planning for Maintenance of instrument: Each equipment vendor through their quality manuals proposes clear plan and methodology for the alteration, cleaning, and other supporting work related to equipment to confirm that quality standards and specifications of manufacturer were met. All the maintenance related work such as servicing, software version changes done by service engineers or in-house engineers shall be documented.
- Periodical Verification: Each instrument vendor should provide timely verification in accordance with pre-established agreement between vendor and equipment manufacturer. All the periodical verification which might include date of maintenance by service engineers shall be documented.
- Establishing Tolerance limits: As a part of calibration and performance verification, every vendor should provide clear tolerance limits for calibration, further their should evidence and scientific rationale for establishing these tolerance limits.
- Computer system verification: If the instrument has automation in its capabilities, then computer system verification should be part of Installation and operational qualification.
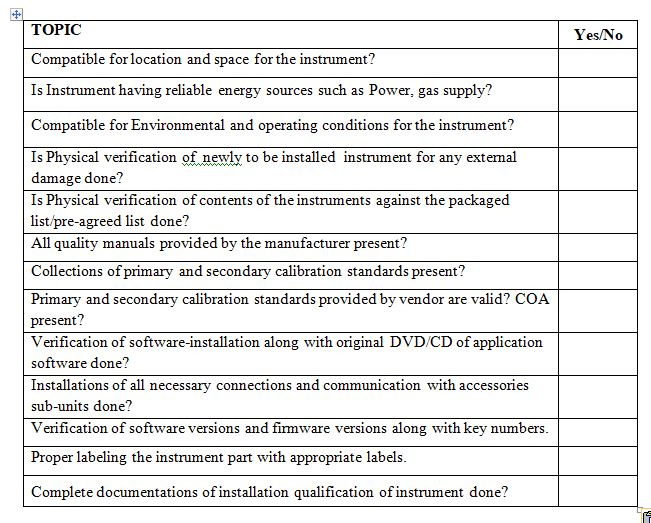
After reading this blog, we hope you can understand the importance of operation qualification and properly use the proposed checklist and improve on it further.
Now that you know this:- hopefully you are in position to answer the Assignment(s)
- Please review the IQ/OQ/PQ of recently installed equipment in your laboratory?
- In your lab, do IQ/OQ/PQ are properly archived? Further easily retrievable at the time of requirement?
- In your lab, quality manuals submitted by Vendor is stored properly and accessible to analyst at the time of requirements?
- Does SOP design based on IQ/OQ/PQ of the instrument?
- Does SOP incorporate preventive maintenance and calibration as per IQ/OQ/PQ or vendor recommendations?
- Is training of laboratory staff part of new IQ/OQ/PQ?